written by Rene K. Mueller, Creative Commons CC BY NC 2014, 2015, 2020, last updated Sat, July 18, 2020
I took the afternoon to sort all ~180 strawbales:
- heavy and compact bales first to use (layer 1)
- good strawbales, a bit ligther as next (layer 2-5)
- moderate good strawbales, light, well bound (layer 6&7)
- and putting aside bad strawbales (~10 bales)
A few strawbales I fixed by re-binding, using additional cords to make it strong again. As mentioned, since I didn't instruct the local farmer to press bales for actual building, the bales are quite light (~15kg) and not that strong.
The advantage of light bales is that the decided procedure using threaded rods to compress bottom 4 layers and then top most (7th) layer again - that the rods can penetrate the strawbales with a bit effort and keeping them straight while pushing down (M10 x 1m are ok, perhaps M12 x 1m would be better choice for next time).
Today I drew some more detailed plans how to proceed building the cabin:
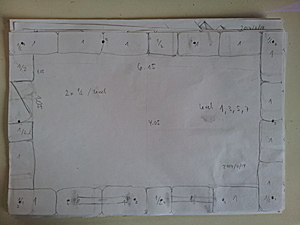
Level 1,3,5 strawbale wall
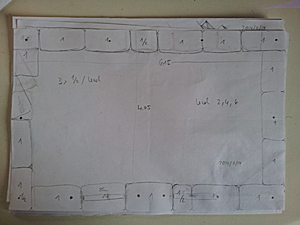
Level 2,4,6 strawbale wall
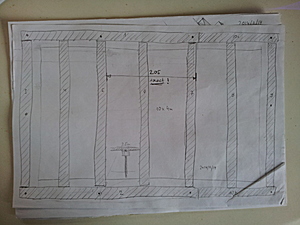
Ceiling plan
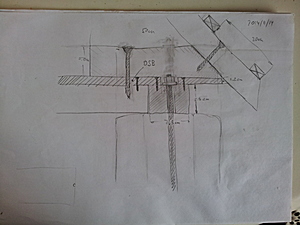
Detail ceiling foot / roof plan
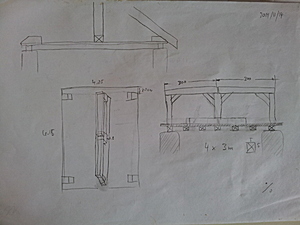
Rough sketch of roof structure
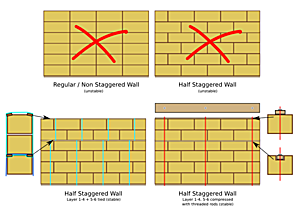  Options to build Strawbale Wall |
Rainy days prevented me to continue, but it gave me more time to plan putting up the walls.
Options:
- putting bales straight on top of each other: highly unstable, 3-4 layers might work
- putting bales half-way shifted or staggered on each layer (like putting together a brick wall), 4 layers might work
- putting bales half staggered half-way, first 4 layers tied together, next 2 layers tied on top of 4th layer: 6-7 layers might work
Some of tests I made:
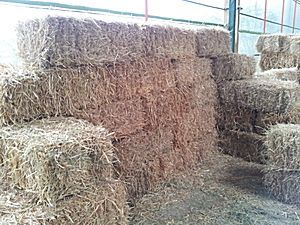
Shifted wall with no support
2014/11/12 11:20
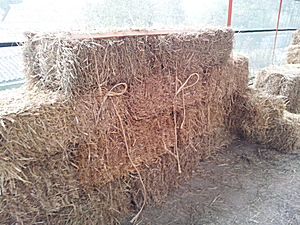
Shifted wall with 4 layers combined
2014/11/12 11:33
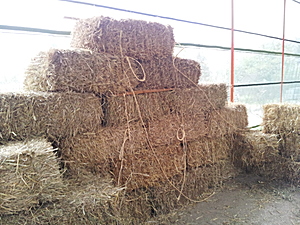
Shifted wall with 4 + 2 layers combined
2014/11/12 11:53
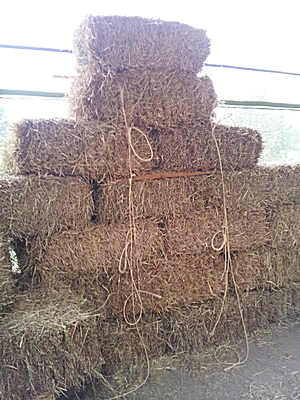
Shifted wall with 4 + 2 layers combined + 1 layer
2014/11/12 11:57
Yet, even the last option gave some improvement, I decided to go with following solution:
Stabilize the wall each 2m distance 3m long M10 threaded rods (total 30 x M10 x 1m, Euro 1.40 / pc) vertically positioned and using nuts at the bottom and top: under the floor, and on top a long piece of wood which presses then the 6 or 7 layers of bales together.
It keeps the bales and wall therefore in position, and gives the possibility to compress the layers together in a controlled way (height-wise).
It's a bit more overhead than I anticipated, but I think it makes the cabin sturdy and less prone to become unstable.
The door I use is exactly 210cm in height, its frame to be precise, so I pondered on follow options:
- 6 layers give apprx. 210cm height, when compressed going near 200cm, and missing 10cm: making door open to outside instead of inside, having 10cm reach over the bales on top.
- 7 layers give apprx. 240cm height, when compressed going near 230cm, still well over 210cm of the door frame, ability to keep the door opening to the inside - filling the expected gap above the door frame of 10-20cm with straw and/or wood.
and I likely go with the 2nd option using 7 layers, as 6 layers with resulting 200cm ceiling height is a bit low for my taste, and I have sufficient amount of bales spare.
With apprx. 23 bales per layer, and 7 layers I reach total of apprx. 161 bales (2.4 tons).
Today, after weeks of delay, the strawbales arrived - so called "small" strawbales, as nowdays "large" 400kg heavy strawbales are sold.
I've got apprx. 180 strawbales in this shipment:
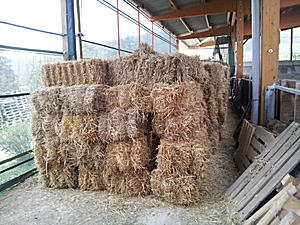
~180 Strawbales
2014/11/09 14:00
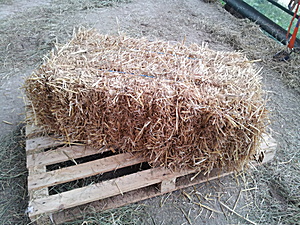
Frontside of Strawbale
2014/11/09 14:01
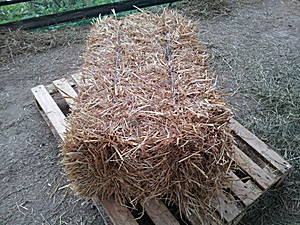
Headside of Strawbale
2014/11/09 14:02
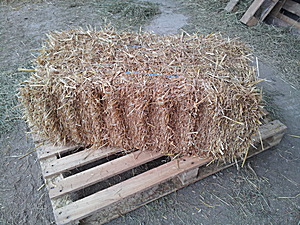
Backside of Strawbale (9 layers)
2014/11/09 14:02
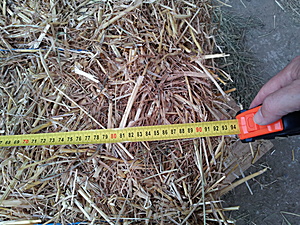
Width ~90cm
2014/11/09 14:02
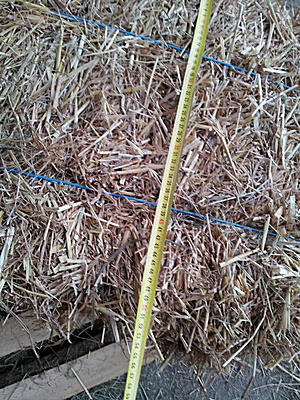
Depth ~50cm
2014/11/09 14:03
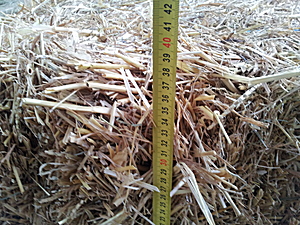
Height ~37cm
2014/11/09 14:03
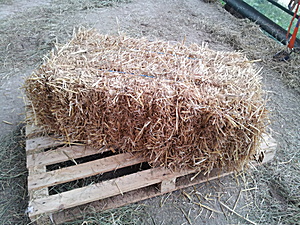  Frontside of Strawbale |
Numbers of a Strawbale:
- Width x Height x Depth: 95cm x 38cm x 58cm (0.21m3)
- Cords: 2 (blue)
- Weight: ~15kg (rather loosely pressed)
- Year of Straw: 2013 (2 years old straw)
I call the "Frontside" where the straw is bent, and "Backside" where the straw is cut and the hollow diameter of the straw exposed - the backside will likely reside inside of the cabin, whereas the frontside outside.
The strawbales are made from 2013 straw, and did cost Euro 3.00 per bale, which is rather expensive, as 1-2 months ago straw 100kg was Euro 8 which are 4-5 heavy bales (Euro 2.00), or ~6 light bales (Euro 1.35).
I've got also got rather light bales, apprx. 15kg. The farmer informed me, if I told him ahead, he would have pressed heavier and compacter bales for me.
About 10% of the bales are misaligned, and the two cords no longer straight, so I expect to "fix" some of the bales again. Based on the photos you see about 9 layers pressed together - the farmer told me he pressed based on 100cm and the final length of ~90cm came from compression.
I also expect about 2cm loss of height when compressed per layer.
So, based on the measure of a sample strawbale I need:
- Width 615cm / 90cm => 7 bales x 2 = 14 bales
- Depth 405cm / 90cm => 4.5 bales x 2 = 9 bales
- which results to ~23 bales per layer
- Height ~210cm / 35cm (compressed) => 6 layers
which results in 6 x 23 bales => 138 bales, about 5 x 3 bales are not needed for door and two windows, which makes 123 bales in total, or apprx. 123 x 15kg = 1.8 tons weight.
Now, the coming week are 1-2 dry days, other days it's exected to rain, so there is enough time to raise the walls, as I expect as my first strawbale cabin I require apprx. 2-3 consective days without rain and fog to raise the wall and assemble the ceiling. The roof can be postponed for a few days.
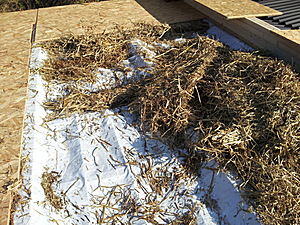  Taking out wet straw insulation, and replace with dry one |
I had to open 2/3 of the floor in order to replace two insulation parts. It's definitely the weak point of this floor setup: any water penetrating the floor is not running away or through, but stays with the straw insulation.
The plus point is though, that there is no humidity coming from underneath into the straw and then the OSB floor.
Last night it began to rain intensesivly, and one of the bitumen parts bent so some rain water leaked on the new floor and through to the straw insulation, and due to the humidity blocker, could not run away - so I relieved it by poking some holes into the PVC.
Yet, I have to remove some OSB and replace the humid or wet insulation straw, before I can continue. The next days will by foggy and partially also rainy - let's see how things go.
Today it was slightly covered sky, apprx. 15-20C warm, and it was possible for me to work longer than just a few hours, but the entire afternoon.
I positioned the OSB as perfect as possible, there were some 1mm gaps at max but mostly I could pushed them closely together, and drilled 35mm screws on the 4m beams underneath, 4 screws per OSB.
As next I cut off the PVC left over and wrapped it under a bit. In order to prepare for the next 1-2 days with some rain expected, I used the bitumen roof parts to cover the floor, as the PVC cover has some holes which would leak water on the floor.
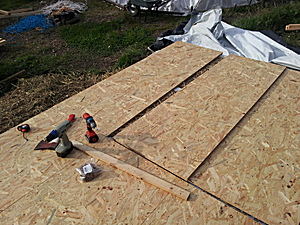
Position the OSB closely, with hammer and a piece of regular cut wood
2014/11/04 14:07
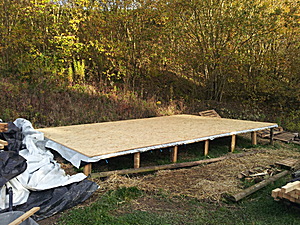
Floor finished, PVC wrapped underneath
2014/11/04 15:34
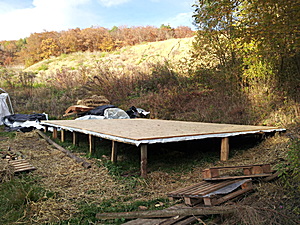
2014/11/04 15:34
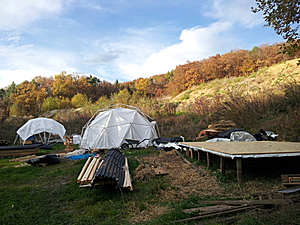
2014/11/04 15:34
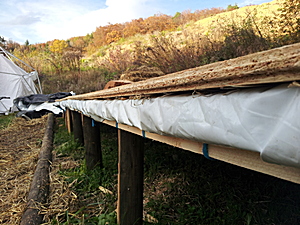
Closeup
2014/11/04 15:35
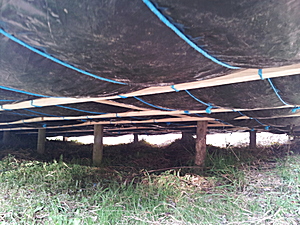
Look underneath with the blue cords
2014/11/04 15:35
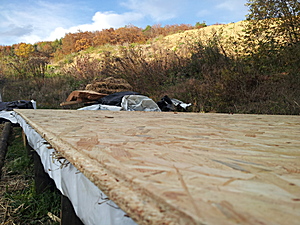
2014/11/04 15:36
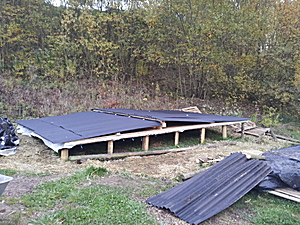
Covering with bitumen roof parts, protecting for the expected rain
2014/11/04 16:46
Tomorrow are finally the strawbale expected, hopefully - yet, the weather as mentioned won't be supportive to continue with the construction, so I wait for 2-3 day window to raise the walls.
Once the walls (and door and 2 windows) are raised, the ceiling can be done quickly, and then, so far my plan, construct the roof on top of the ceiling within a day.
Adding and removing some straw to level it properly, and roughly position the OSBs:
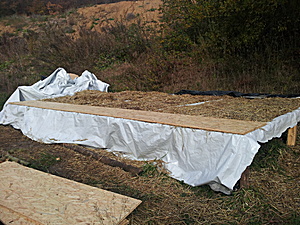
Starting to lay it out
2014/11/03 14:18
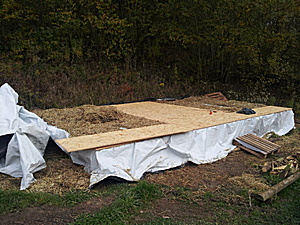
2014/11/03 15:02
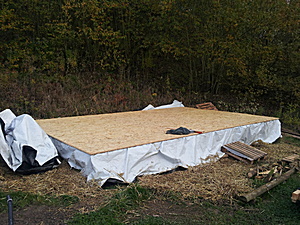
Roughly positioned, not yet fixated
2014/11/03 15:48
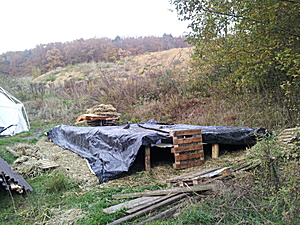
Covering it up for the night
2014/11/03 15:56
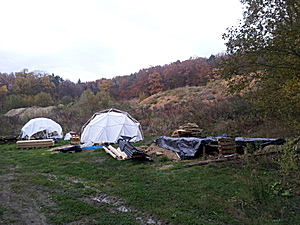
2014/11/03 15:56
Since the wooden strut as enforcement turned out too thick under the floor insulation, I came up with the idea to use cords to wave a kind of net in between, then the PVC cover, and then the pressed straw layers:
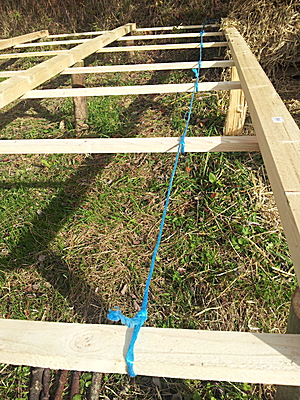
Using a cord to wave a tighter or closer support
2014/11/02 13:16
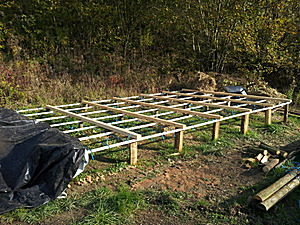
Cord net finished
2014/11/02 14:02
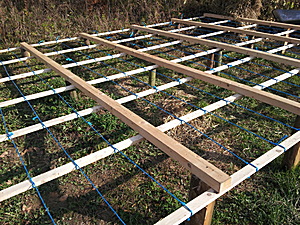
Cord net finished (closeup)
2014/11/02 14:02
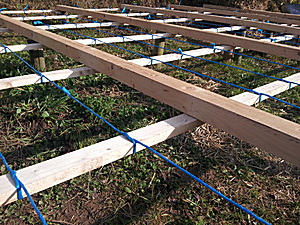
Cord net finished (closeup)
2014/11/02 14:02
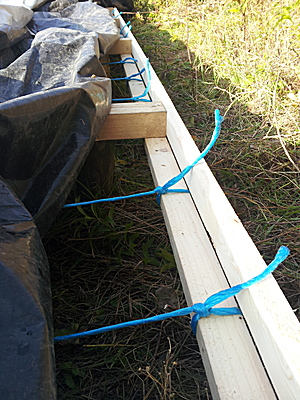
Vertical end strut
2014/11/02 14:36
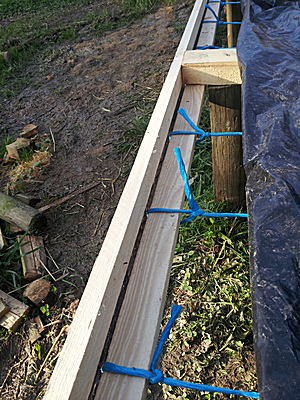
2014/11/02 14:40
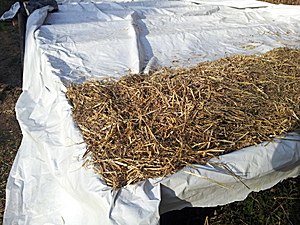
Refilling the straw layer
2014/11/02 14:41
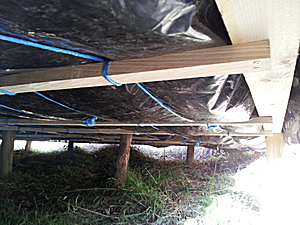
Looking underneath
2014/11/02 14:42
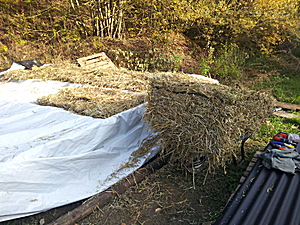
Continuing putting pressed straw layers
2014/11/02 14:52
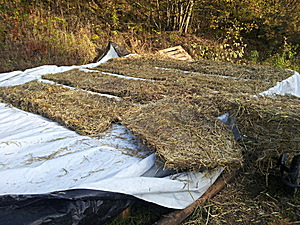
Some layers are compact, but still fragile to handle (tend to fall apart)
2014/11/02 15:07
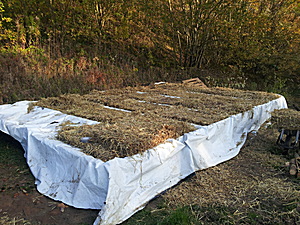
Almost done for today
2014/11/02 15:29
I'm going to loose the pressed straw layers so they use up more volume, yet, the OSB can easily press it again, to make sure entire dedicated space is filled with straw.
It's quite foggy at mornings, around 12:30 to 13:00 the sun penetrates the fog and disolves the remaining fog, until 15:30 I have direct sunlight, afterwards the sun sets behind the trees and humidity falls on the surface - so limits the time to work on the cabin to about 2-3 hours per day.
Today I laid a strong PVC canvas over the grid, and laid some straw over it - the pressed straw layer from a large strawbale (1.5m x 0.8m x 0.6m ~ 400kg) is about 90cm wide, and 8cm thick pressed, ideal for my use case.
I used 3 layers for one "lane" of my grid. Some additional support is required which I will do with cords tomorrow.
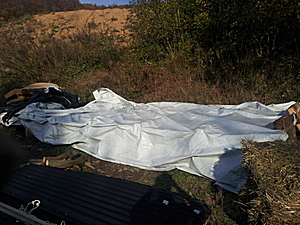
PVC canvas as humidity blockage underneath
2014/11/01 14:34
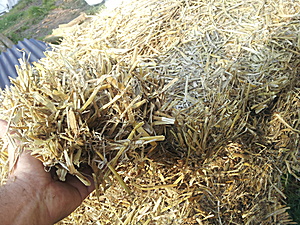
Single layer of pressed straw
2014/11/01 14:34
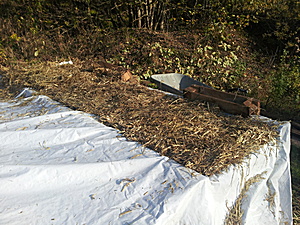
One lane of the grid with straw layers filled
2014/11/01 14:39
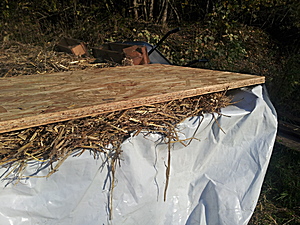
Testing with OSB over it
2014/11/01 14:46
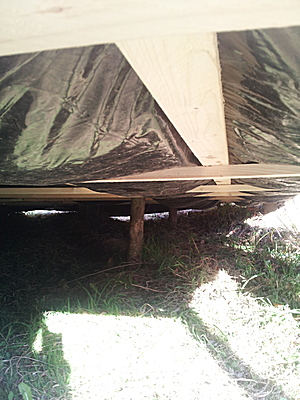
Supporting strut, but it's too thick
2014/11/01 14:46
I finished the supporting grid for the insulation, and tested with some China Grass based insulation matt - unfortunately it's a bit too thick for my use case:
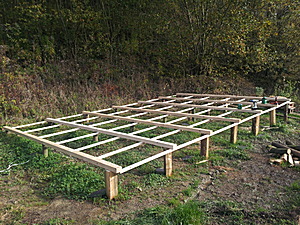
Floor grid finished
2014/10/31 14:00
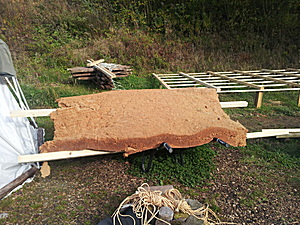
Testing with China Grass based insulation matt
2014/10/31 14:01
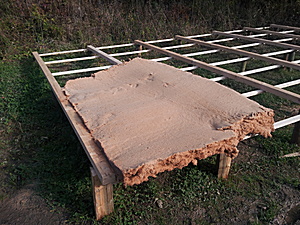
2014/10/31 14:10
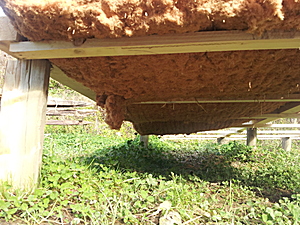
2014/10/31 14:10
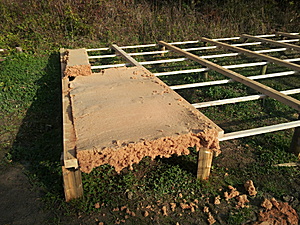
Making it fit, but it's too thick
2014/10/31 14:23
I used smaller struts and attached them beneath the main floor beams, to prepare the floor insulation:
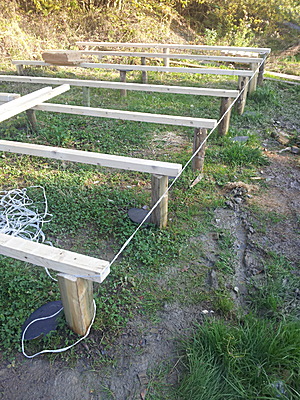
Aligning the beams before fixating
2014/10/29 15:01
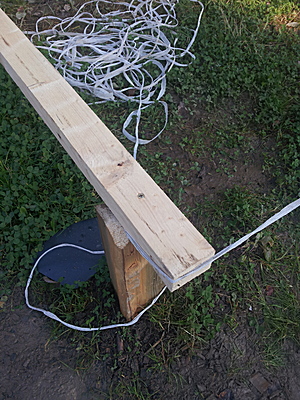
2014/10/29 15:01
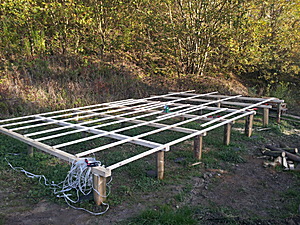
2014/10/30 15:18
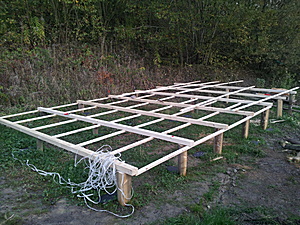
2014/10/30 16:51
The idea is to use some plastic and then put the insulation on it and then the floor 22mm thick OSB.
The strawbales should arrive within the next week, so I decided to continue with the floor construction:
- precisely aligned the beams, properly parallel with perpendicular alignment for the OSB, +/- 1cm correctness is mandatory, as I don't have much margin
- fixated the 4m beams with 80mm long screws
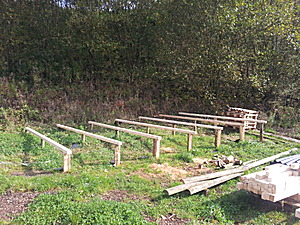
Laying on the main floor beams (7 x 4m long)
2014/10/24 13:27
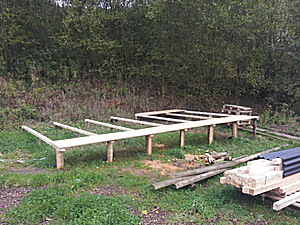
Testing with OSB
2014/10/24 13:44
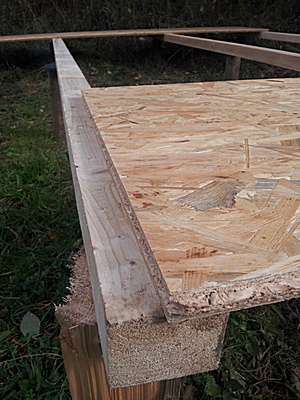
Needs to be pretty exact (+/- 0.5cm)
2014/10/24 13:57
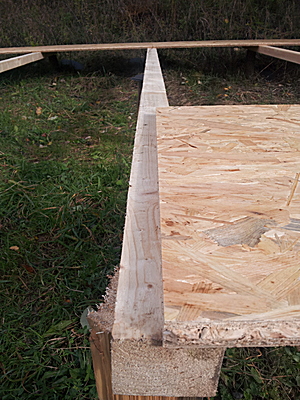
2014/10/24 13:58
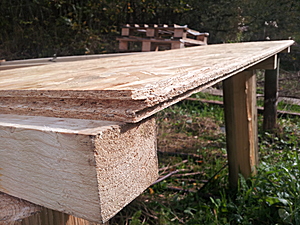
2014/10/24 13:58
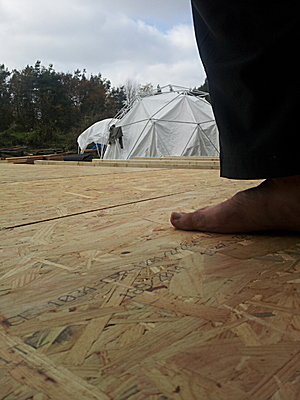
2014/10/24 14:11
Where I am there are spare insulation material, apprx. 3m x 1.2m and 30cm thick and soft, when transporting they tend to "break" - I gonna try these, and if they don't work I gonna use loose straw to fill the space.
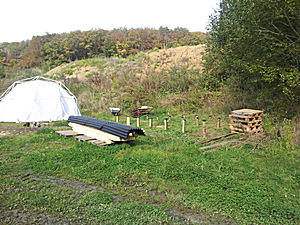  3 x 7 ground poles rammed into the ground, leveling the floor |
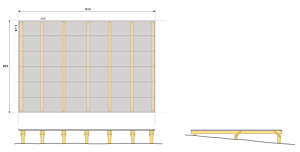  Base Plan |
I decided to ram poles into the ground, apprx. 30-40cm deep. This has the advantage of strong and solid footing, and also not sealing the ground at all.
It was a bit tricky to ensure perpendicularity, but it was achieved by measuring with a cord the diagonal both ways until they were the same length.
The distance between the poles were easily to measure. Once they were rammed into the ground, either hammered further or cut and then with a 4m beam leveled until it fit.
It was a bit time- and physical strength consuming but forth the efforts.
The next steps I had to postpone as the strawbale delivery was delayed and I planned to build the cabin within a few days with sun and no rain, so I don't have to cover up the unfinished construction.
Some notes of mine on paper (also for my own reference):
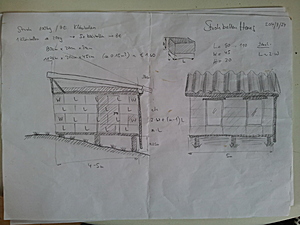
Rough sketch of cabin
2014/11/03 09:39
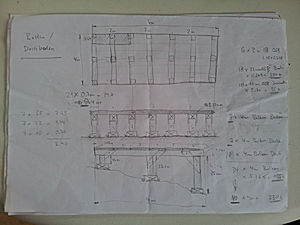
Some details of floor support
2014/11/03 09:39
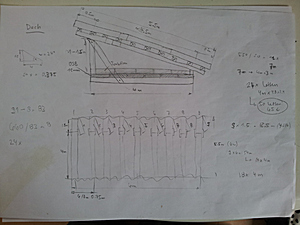
Single slide roof sketch
2014/11/03 09:40
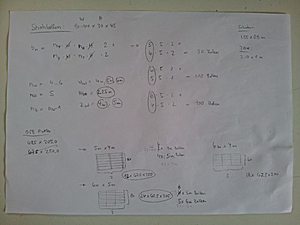
Optimizing size of cabin based on strawbale size & OSB size
2014/11/03 09:40
and electronic counterpart:
After some pondering I defined the base or floor size based on the OSB and main beams which are 4m long, which made the depth, the width I came up 3x OSB length-wise 3x 2.05m = 6.15m and 6x 0.675m = 4.05m - perfect.
(End of Article)Content:
- Page 1: Plans, Numbers, Material, Reflection
- Page 2: Diary, 2020/01/07: This Is The End, 2017/04/12: Earth Oven (1), 2017/04/09: Spring, 2017/03/05: Sunny Day ...
- Page 3: 2015/01/03: Snow Slide Down, 2015/01/01: New Year, 2014/12/31: Week with Snow, 2014/12/27: First Snow ...
- Page 4: 2014/11/18: Sorting Strawbales, 2014/11/14: Planning Procedure, 2014/11/12: Planning the Walls ...